ヘルメスの強みstrength
当社の前身は、硬質発泡ウレタンが1960年代に初めて日本に紹介された頃から成形品の製造に取り組んできました。
その間、多くのお客さまのさまざまなアイデアを具体的で詳細な表現を持つカタチにしてきました。
硬質ウレタンが持つ高い汎用性と多様な用途についてご紹介します。
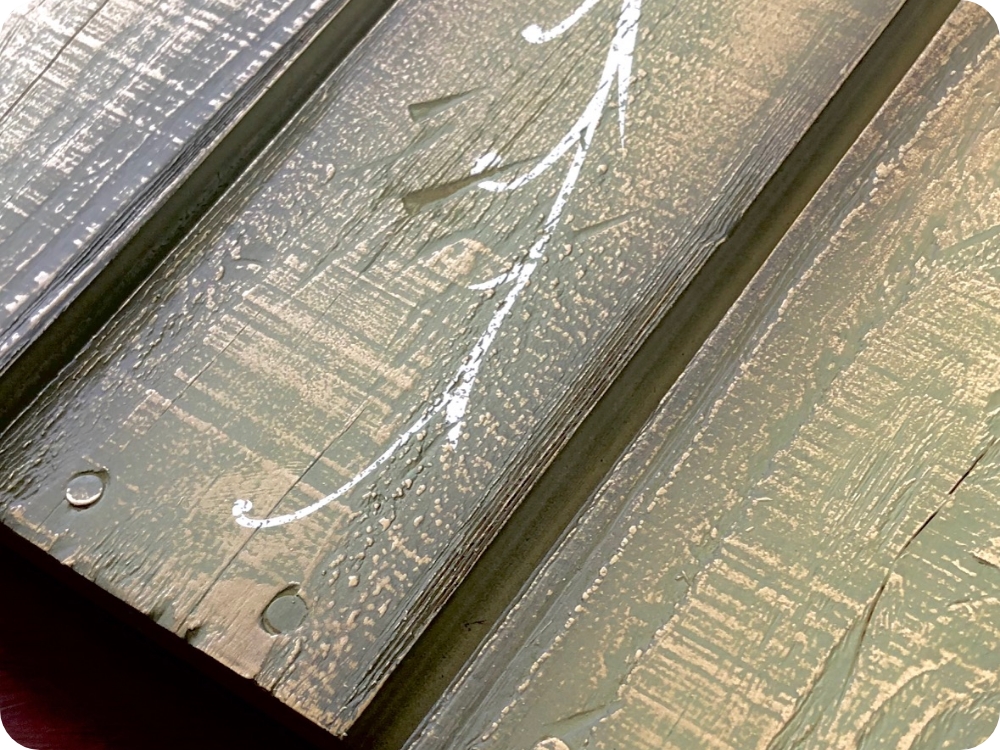
リアルな質感再現
実際のマスターモデル(元となる型)からシリコーンゴムで型取りをして成型する当社の製法では、マスターモデル素材の質感をそのままリアルに再現することが可能です。そのリアルな質感に当社独自の技術による塗装を施すことにより、ほぼ本物と同じ感触でありながら、本物以上の耐久性と耐水性を誇るリアル成型品による量産が可能です。この製法によりお客さまが持っている無限のアイデアを実現することが可能になります。例えば、朽ちた木目の質感や、釘打ちで貼り合せてあるように見えても実は一体成型でできた木箱など、本物素材では量産ができない製品もリアルに再現されて量産が可能です。用途は文字通り無限大です。
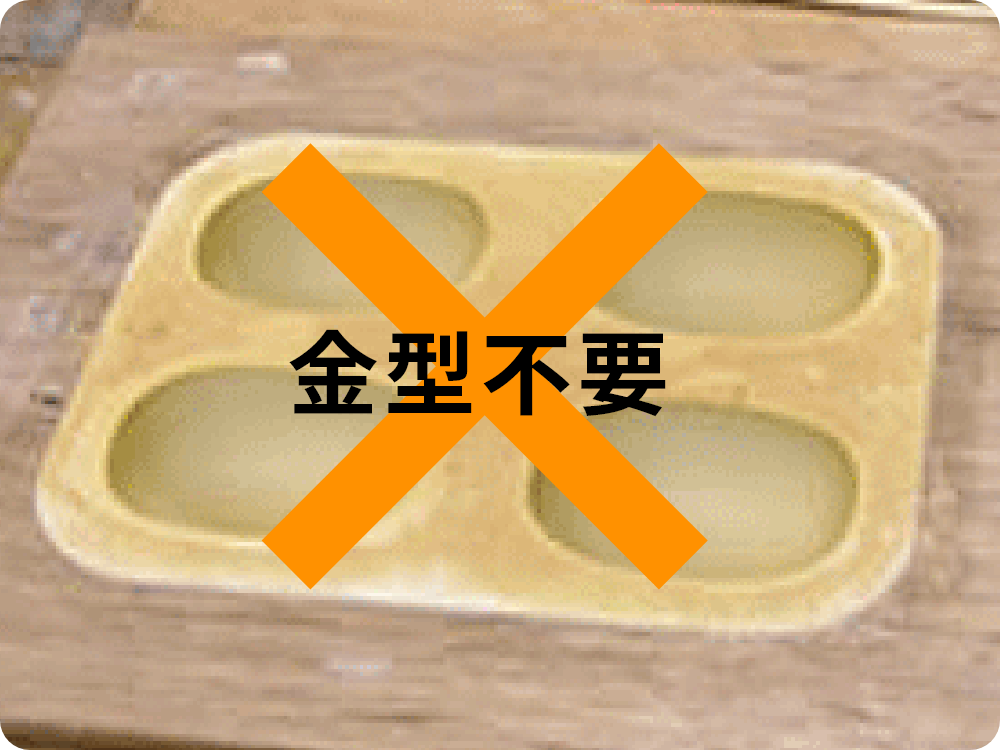
小ロットでも高価な金型は必要ありません
一般的に成型品には金型が必要と思われがちですが、金型(モールド)が必要とされるのはABSのような汎用プラスチックの成型品の大量生産(数千個単位のロット)においてです。ヘルメスでは、独自のシリコーンゴムで作成した型を元に、数十から数百個の生産ロットでの硬質ウレタン成形品を「試作以上、量産未満」の生産形態でお届けしています。金型の製作には多額のコストが必要で、そのコストを回収するには大量生産が必要です。一方、硬質ウレタンの場合、単体の成形品の製造コストは射出成型による量産品よりは割高になりますが、小ロット生産という型代を含んだトータルコストで見た場合には非常に優れたコストパフォーマンスが実現します。個生産に特化した3Dプリンターで製造するには数が多く、大量生産するほどの量は必要ないという場合、当社の硬質ウレタン成型品がうってつけです。実用性は文字通り最適です。
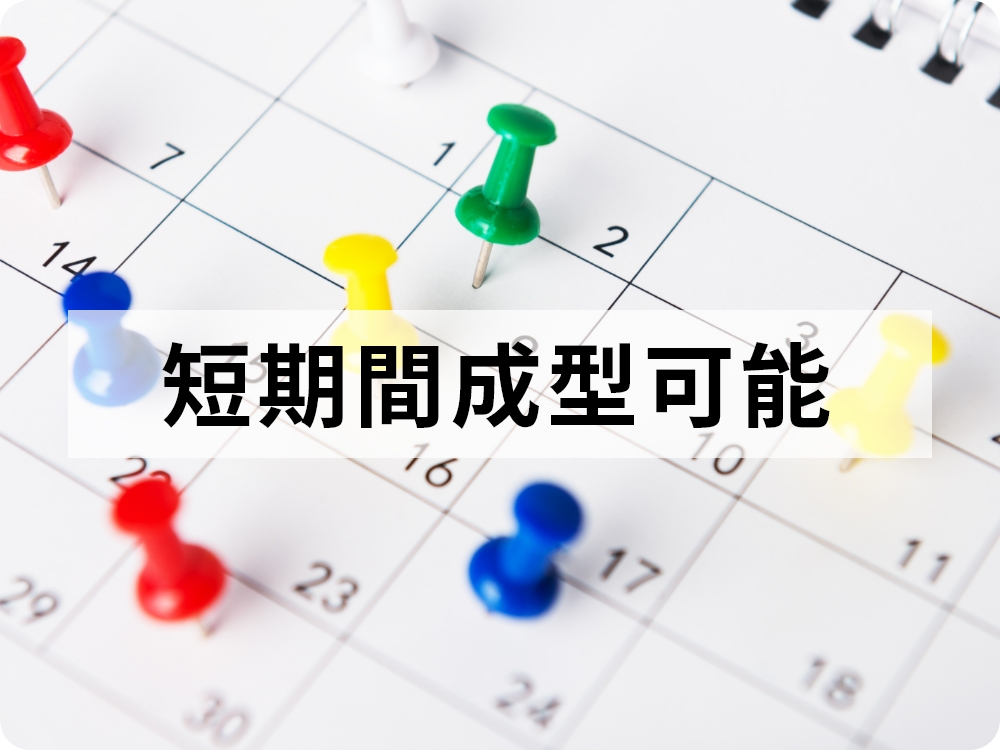
短期間での成型が可能
金型の作成にはコストだけでなく多くの時間と手間がかかりますが、硬質ウレタンの型は短時間で硬化するシリコーンゴムで作成します。バレンタインの手作りチョコのシリコーンの型を想像していただければ理解しやすいと思います。成形品は、比較的柔らかいシリコーンゴムを剥がして取り出すので、金型による成型の場合の、取り出しのプロセスで制限が生じるような複雑な形状のモデルであっても比較的容易に成型することができます。柔軟な形の成型と短期納品が可能な硬質ウレタンは、「工業製品」以上、「芸術作品」未満の高い品質を実現します。
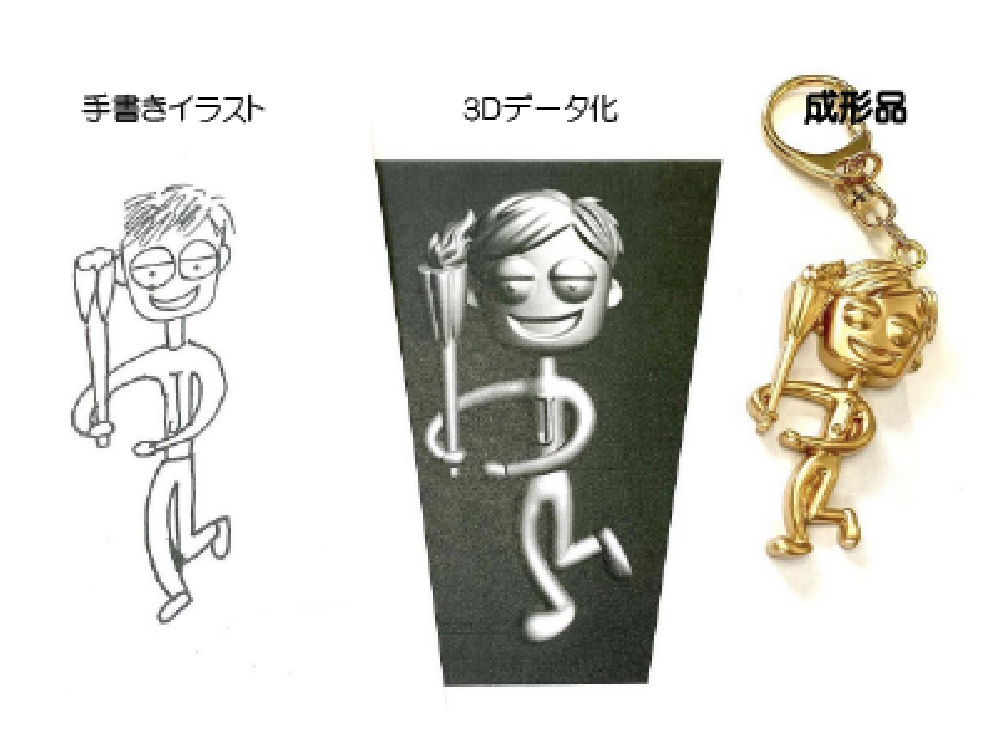
イラストからの具現化も可能
シリコーンゴム型の作成には3Dのマスターモデルを使用しますが、2Dのイラストからでも3Dの成型品を作成することが可能です。ご提供いただいた2Dのイラストはモデリングソフトで3D化され、切削加工や3Dプリンターで立体的なモデルとして製作されます。このモデルをマスターモデルとして使用することにより、「試作以上」の量産試作が可能になります。アイデアを実現する可能性は文字通り無限大です。
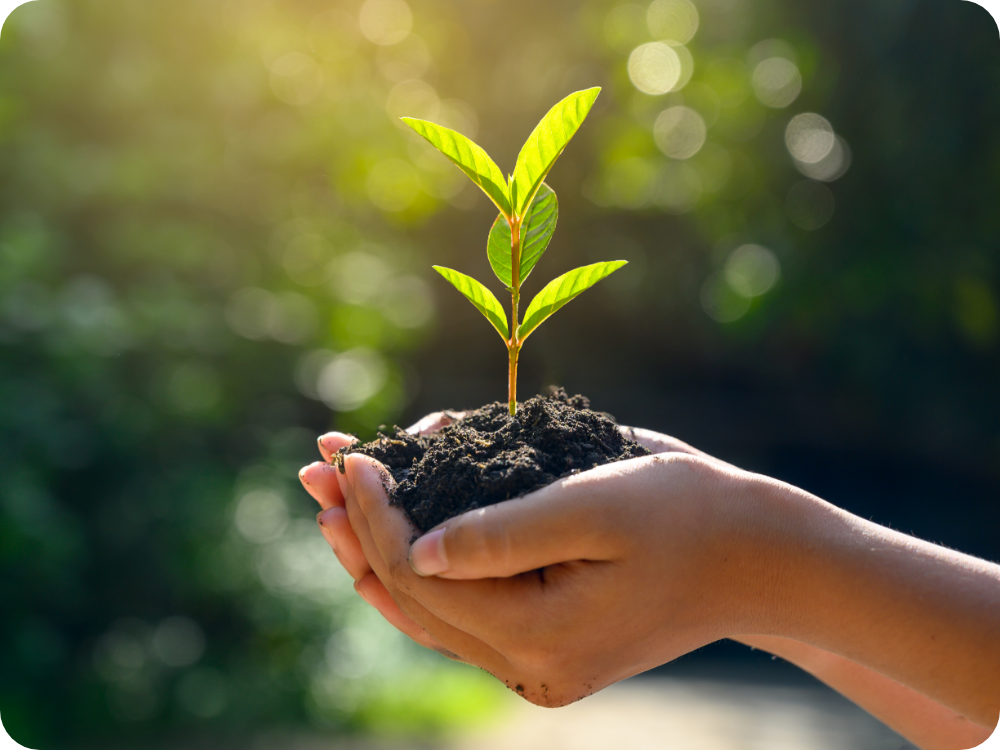
環境にやさしいノンフロン製法
発泡硬質ウレタンは、その内部のきめ細かい無数の気泡を特長とします。この気泡によって高い断熱性や耐久性、そして軽量性といった特性が生まれます。従来の硬質発泡ウレタンの多くでは、この気泡を生成するためにフロンガスが使用されてきました。しかし、フロンガスの使用が規制されている今日、代替フロンの使用も認められてはいますが、ヘルメスでは業界に先駆けて1989年からフロンおよび代替フロンをまったく使用せずに、水で発泡する原料を使用してきました。ノンフロンタイプの発泡硬質ウレタンは、廃棄時に焼却しても有害なダイオキシン類が発生しません。
ヘルメスは、SDGsが謳われるずっと以前から高い環境意識の下で製造を行ってきました。汎用プラスチックをはじめとするさまざまな素材の代替製品として、将来におけるサステナビリティを実現する能力は無限大です。